OZM340-10M OTF &Transdermal Patch Making Machine
Product Video
Sample diagram
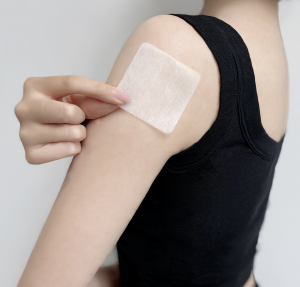
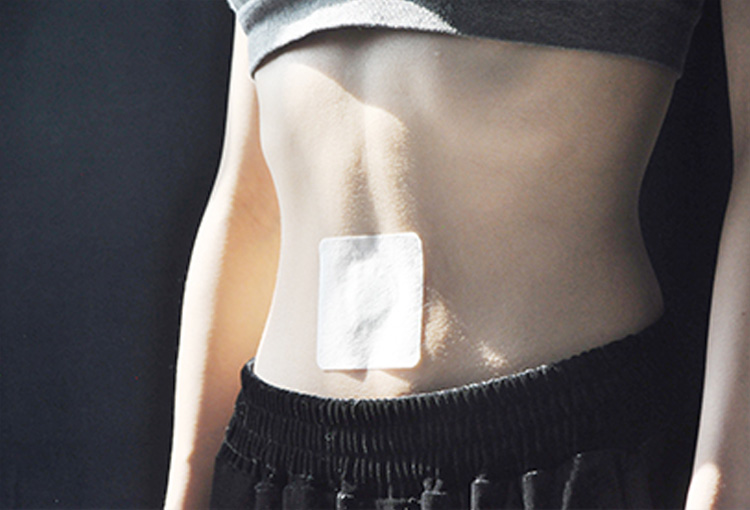
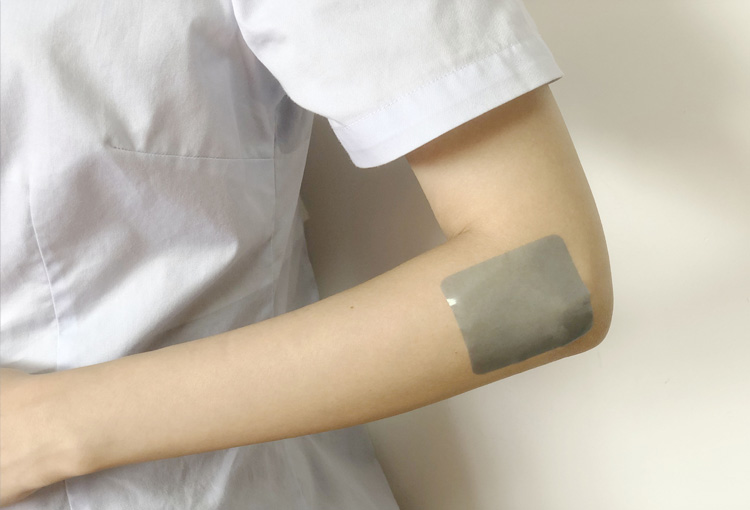
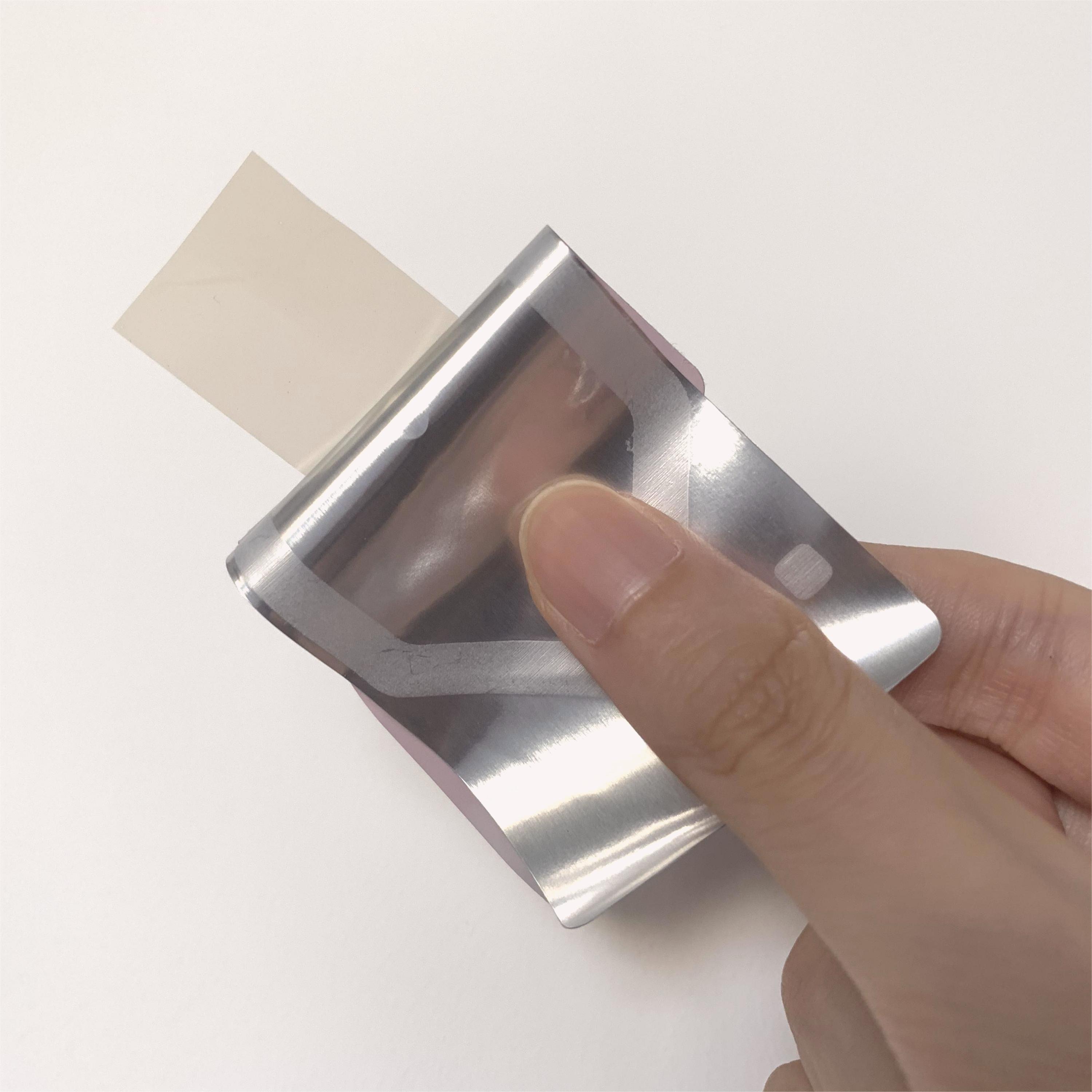
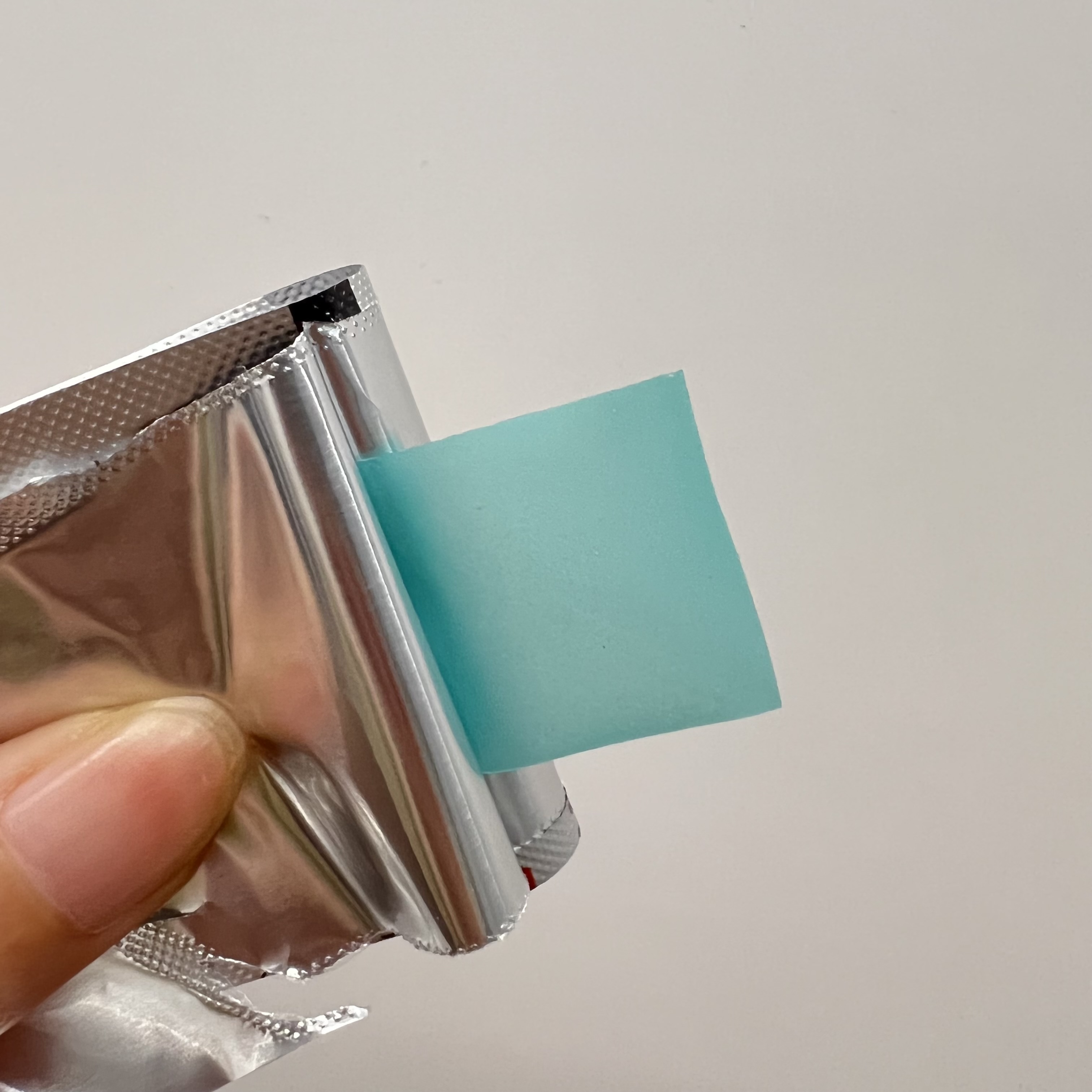
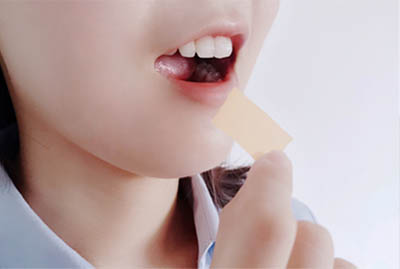
Performance & Features
1. It is suitable for the composite production of paper, film, and metal film coatings.The power system of the whole machine adopts a frequency converter stepless speed regulation system. Unwinding adopts magnetic powder brake tension control
2. Adopt main body plus accessory module structure, each module can be disassembled and installed separately. Installation using cylindrical pin positioning, screw fixation, easy assembly.
3. The equipment has automatic working length recording and speed display.
4. Independent partition of drying oven, with independent automatic control of temperature, humidity, concentration and other functions, to ensure efficient and high quality production.
5. The lower transmission area and upper operation area of the equipment are completely sealed and isolated by stainless steel plates, which avoids cross-contamination between the two sections when the equipment is working, making it easier to clean.
6. All the parts in contact with the material, including the pressing roller and the drying tunnel, are made of stainless steel and non-toxic materials, which meet the requirements and specifications of "GMP". All electrical components, wiring and operation schemes comply with "UL" safety standards.
7. Equipment emergency stop safety device, improve the safety of the operator in debugging and mold change.
8. It has a one-stop assembly line for unwinding, coating, drying, laminating and rewinding, with smooth technology and intuitive production process.
9. The switchboard adopts split structure, and the drying area can be customized and lengthened to make the operation more smooth.
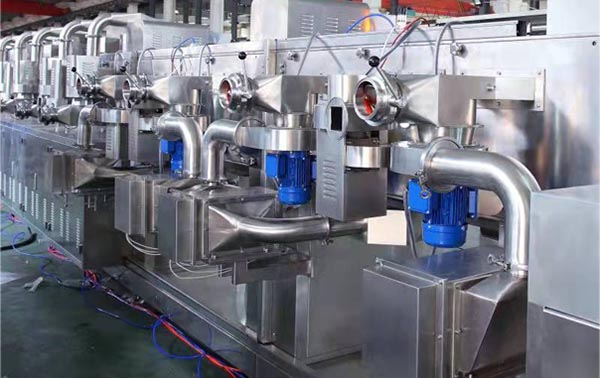
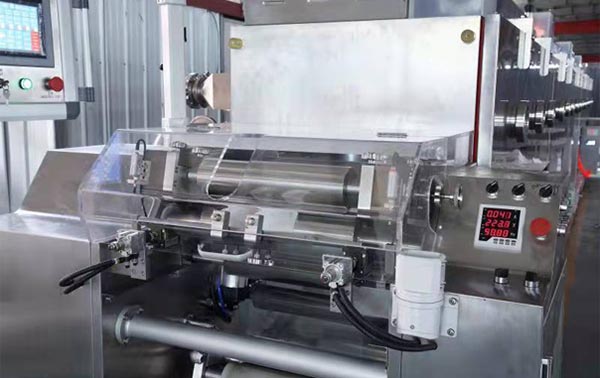
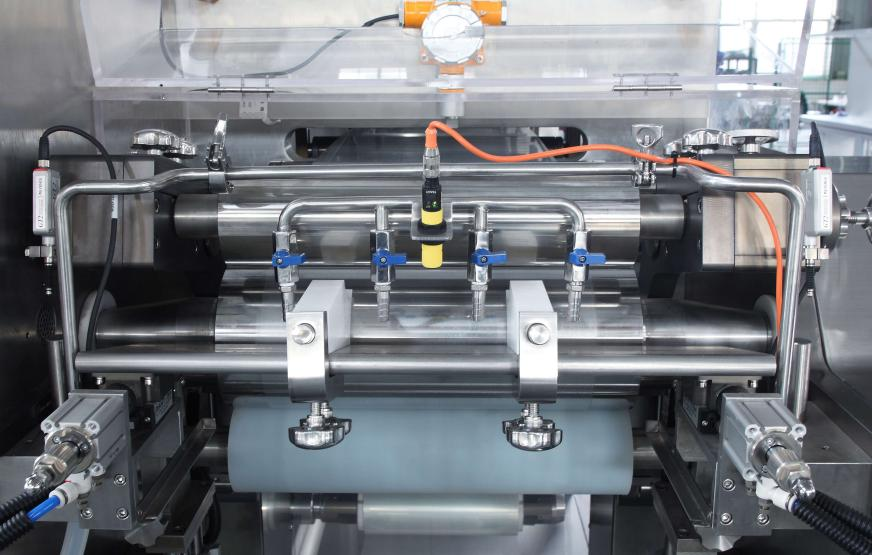
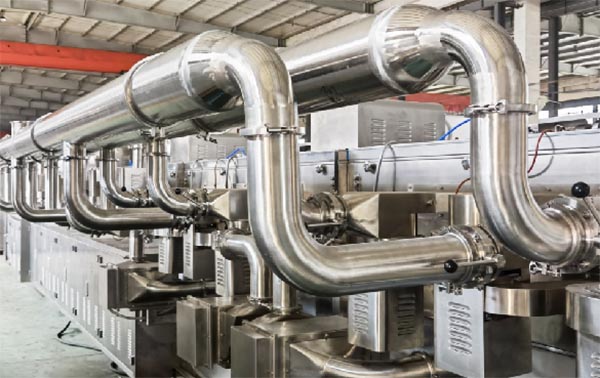
Work station details
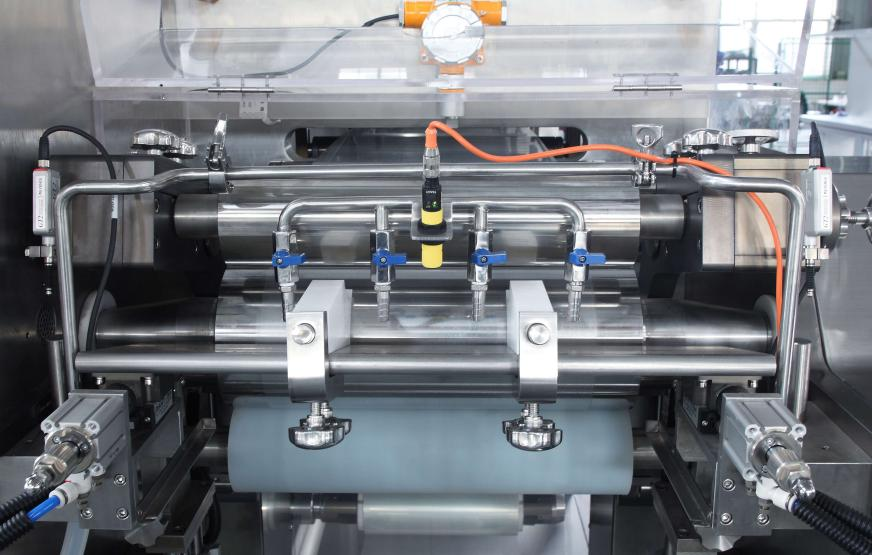
Film head area
1. Comma scraper type automatic film-making head, the coating is uniform and smooth.
2. Automatic feeding method of peristaltic pump
3. The coating width of the film-making head can be adjusted to avoid waste of raw materials;
4. The thickness of the film is adjusted by servo, and the thickness can be completed by inputting the thickness on the touch screen.
Unwinding and rewinding area
1. All adopt the positioning of the air expansion shaft, which is convenient for replacing the film roll;
2. Both are equipped with a film roll tension control system to keep the bottom film in a tensioned state;
3. At the same time, it can be equipped with a deviation correcting device to keep the bottom film from going left and right during operation.
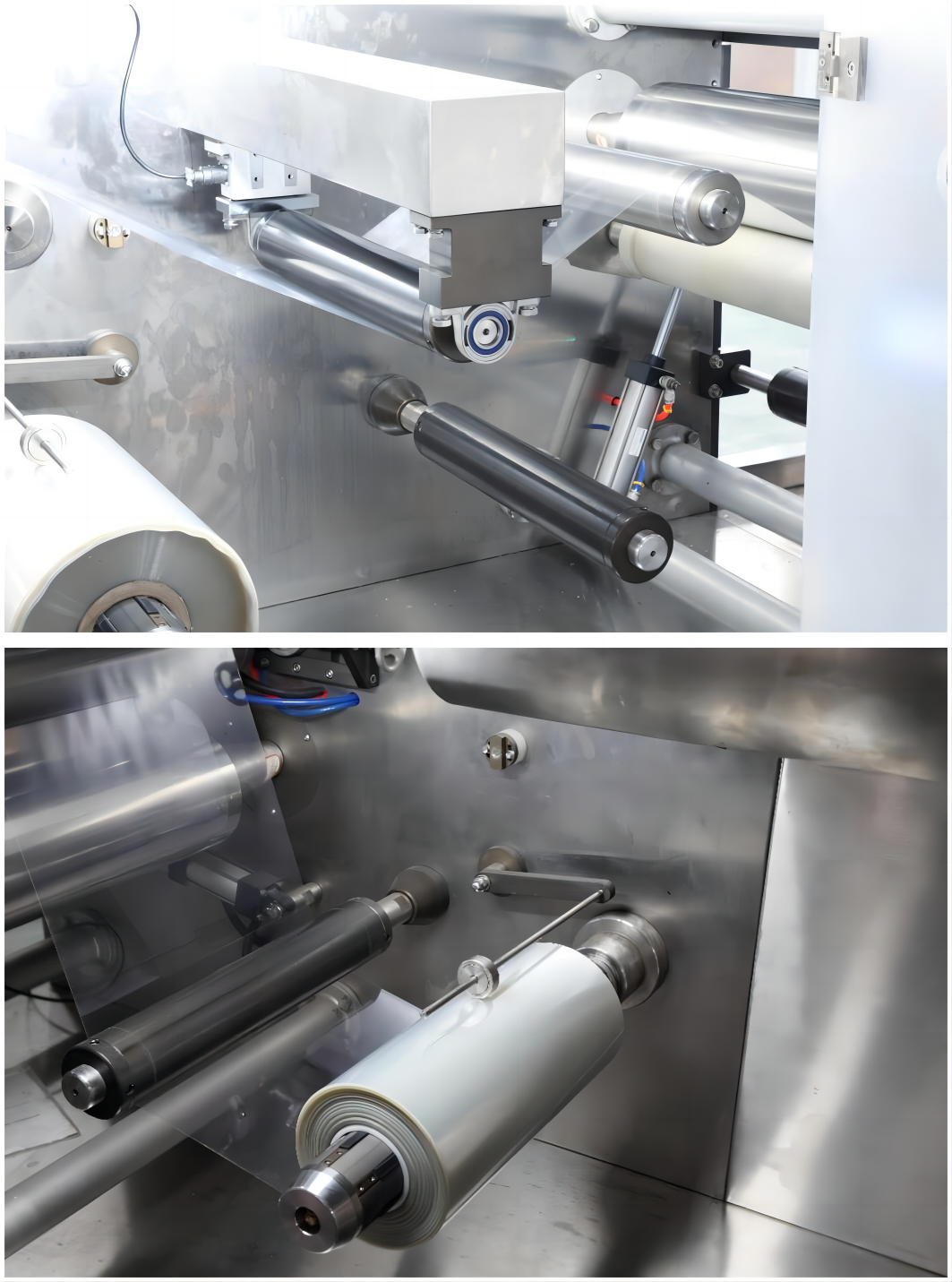
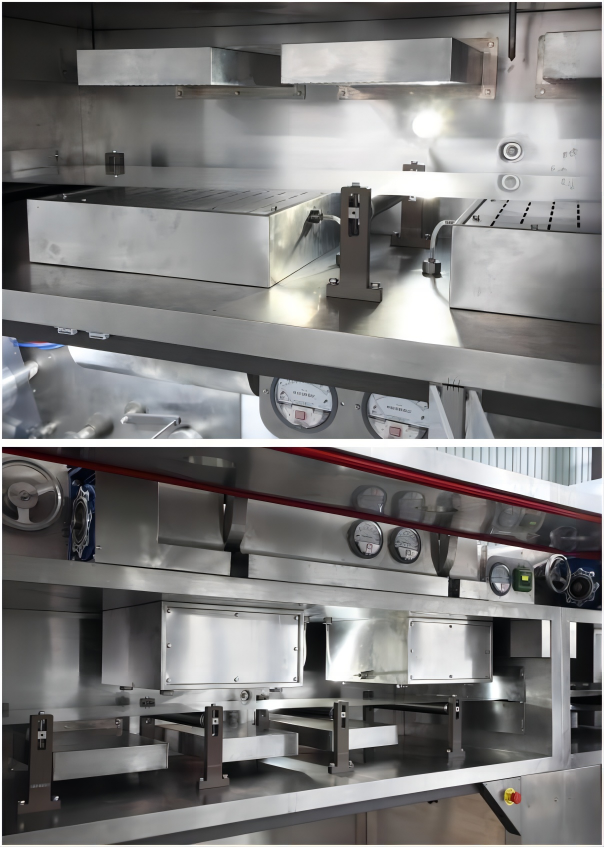
Dry area
1. Independent modular drying area, the length can be designed according to customer needs, the fastest drying speed can reach 2.5m/min;
2. Built-in temperature, humidity, solvent concentration sensors, and through the PLC system control to ensure the internal environment is stable and safe;
3. Built-in H14 grade HEPA high-efficiency filter to ensure that the heated air complies with GMP require;
4. Equipped with a safety protection door to ensure the safety of personnel during operation and prevent the influence of heat inner package workshop to reduce heat loss.
HMI
1. 15-inch true color touch screen with data backup function, IP54 grade;
2. The device account has a 3-level password function, and the graphical overview of the whole machine is easy to operate each station;
3. The control system has the function of electronic signature and audit trail, which complies with FDA's requirements for calculation Machine authentication requirements.
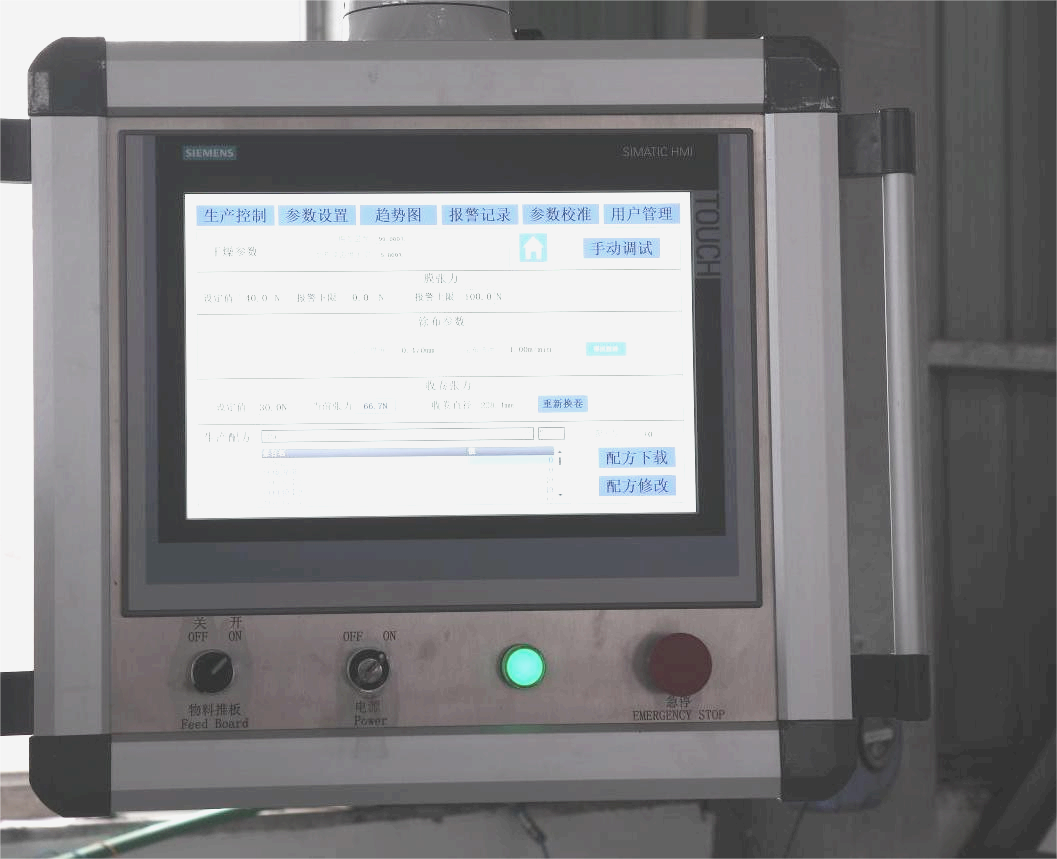
Technical Parameters
Production width | 280mm |
Roll surface width | 350mm |
Speed | 1m-2.5m/min Depends on the actual material and status |
Unwinding diameter | ≤φ350mm |
Rewinding diameter | ≤φ350mm |
Heating and drying method | Built-in hot air drying, centrifugal fan hot air exhaust |
Temperature control | RT-99℃ ±2℃ |
Edge thickness | ±1.0mm |
Power | 60KW |
External dimensions | 9000*1620*2050mm |
Voltage | 380V 50HZ |